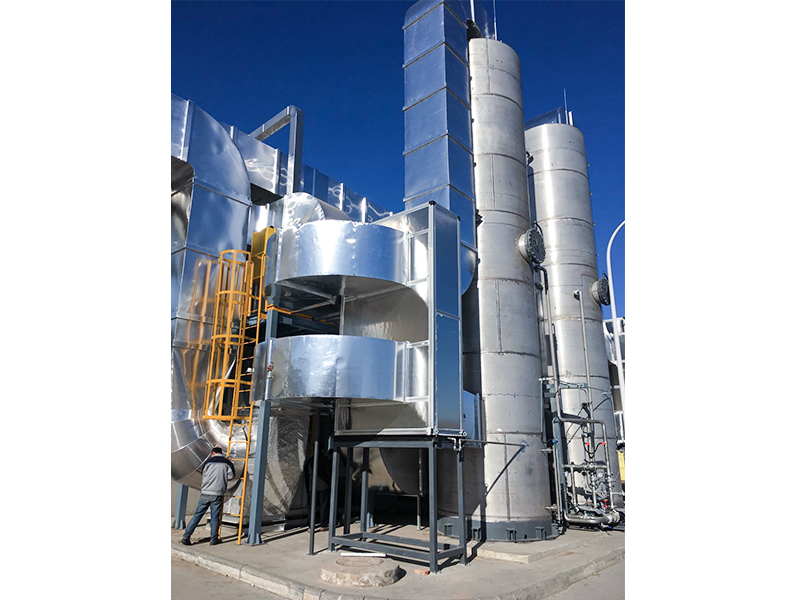
Thermal conductivity significantly affects the efficiency of lithium battery dry rooms. Thermal conductivity refers to the ability of a substance to transfer heat, determining the speed and efficiency...
READ MOREThermal conductivity significantly affects the efficiency of lithium battery dry rooms. Thermal conductivity refers to the ability of a substance to transfer heat, determining the speed and efficiency...
READ MOREThe drying efficiency of lithium battery dry rooms mainly depends on several aspects, which collectively determine the speed, effectiveness, and energy utilization efficiency of the drying process: D...
READ MORELithium battery dry rooms play a crucial role in the development of the new energy vehicle industry. Here are several key aspects in which lithium battery dry rooms contribute to the development of th...
READ MOREThe design of an NMP solvent recovery system can be customized to accommodate changes in process requirements across different industries by considering various factors related to solvent properties, ...
READ MOREThe NMP solvent recovery system comprises several key components, each serving a specific role in the recovery process. These components work together to efficiently remove NMP solvent from process st...
READ MOREEnsuring safe handling of solvent vapors and recovered NMP (N-Methyl-2-pyrrolidone) is paramount in NMP solvent recovery systems to protect both workers and the environment. These systems incorporate ...
READ MOREPharmaceutical dehumidifiers typically use a refrigeration-based or desiccant-based process to effectively control humidity levels in storage areas and manufacturing facilities. The specific process e...
READ MOREExcessive dehumidification in a human comfort-centered surroundings the usage of low dew point dehumidification units could have several ability results: Dry and uncomfortable indoor air: Low dew poi...
READ MOREPreventing excessive dehumidification in low dew point dehumidification units is crucial to avoid potential issues such as overly dry conditions, equipment damage, and increased energy consumption. He...
READ MORELow dew point dehumidification units are designed to achieve a high level of precision in controlling humidity, typically measured in terms of dew point temperature. The dew point is the temperature a...
READ MOREMitigating corrosion on steel components inside Lithium Battery Dry Rooms involves a mixture of careful layout, material selection, and environmental manage. The intention is to create an surroundings...
READ MORELithium Battery Dry Rooms, additionally referred to as dry rooms or dry chambers, are designed to provide a managed surroundings for the manufacturing, storage, and checking out of lithium-ion batteri...
READ MOREHANGZHOU DRYAIR TREATMENT EQUIPMENT CO.,LTD has developed a wide variety of dessicant dehumidifier products according to market demand and guest requirement. 1.Humidity control requirements of air con...
READ MOREThe three-day 15th Shenzhen International Battery Technology Exchange/Exhibition (CIBF2023) ended successfully on May 18th at Shenzhen International Convention and Exhibition Center. CIBF2023 has 1...
READ MOREIn order to enrich the spare time activities of the company's staff and improve their work motivation, the company's labor union held the first Jereh Cup staff tug-of-war outside the company's worksho...
READ MOREIn order to stimulate the work enthusiasm of sales staff, improve the language expression and communication ability of sales staff, on November 12, 2011, Jereh's first sales speech contest was held i...
READ MORE